A Design Worthy of Gold
This article was written by Jacob Holmes and originally published in the January 2025 edition of the Scottish Paddler magazine.
I'm Jacob, a wild water racing paddler and research engineer at the National Composites Centre (NCC). In my role, we assist companies with developing products and processes made from composites. Composites are materials like epoxy that have been reinforced with fibres like glass, carbon or kevlar, and are what most racing boats are made from due to their very high stiffness and strength properties, but very low weight.
This is an exciting job which can involve working on anything from the next generation of aircraft wing to 'the incredible dog shower' (look it up, it's brilliant).
Four years ago, ahead of the Tokyo Olympics, the World and Paralympic champion Emma Wiggs reached out to ask if we could take a look at her paddle to improve it and give her an edge over the competition. This was just before I joined the NCC but the team were able to optimise the blade angle and layup (format and orientation) of the fibres to increase the efficiency of Emma's power transfer, while giving her an incredibly light paddle, which she used to win gold in the VL2 category.
Fast forward to December 2023 with the upcoming games in Paris fast approaching. Emma reached out to the NCC again, this time to see how we could improve her seat. Thankfully, and I suspect uncoincidentally, this project fell to me to lead. I started by calling Emma to understand what it was she needed from a new seat. In summary, Emma liked the shape of her existing seat but wanted it to be lighter and support her more securely, to allow her to transfer as much power to the boat as possible. This last part is an interesting challenge as from a young age I have been taught to drive through my feet to make the boat go faster, but due to Emma's disability, we focussed on the next lowest point of connection, which is the waist strap and hip supports.
Alongside a talented NCC graduate, I then travelled to Nottingham and gathered data by having Emma paddle on an ergo while sitting on a pressure mat. This allowed us to understand how Emma applied force to the seat which would allow us to optimise the transfer of this force to the boat. We also took a 3D scan of her current seat to allow us to build a computer model of the seat.
We could then apply these forces we had gathered to the computer model to optimise the layup. The performance of composites are very dependent on how they are made so this optimisation allowed us to place materials only where we needed it (to keep the seat lightweight) but also to orient the carbon fibres in the direction that the forces would be transferred so that this was as efficient as possible.
With the computer model, we were also able to design a new mould for the seat which we then laid up the carbon fibre onto and cured it in an autoclave (big pressure cooker). We delivered this seat to Emma at the end of March. This new seat was about three times stiffer in key areas than her old seat and 300g lighter.
However, I knew we could do better. When designing a component you have to make a number of assumptions which in engineering tends to sway you to be more conservative, i.e. making something stronger (and therefore heavier) than it needs to be. I therefore pitched a second phase of the project where the NCC could develop and showcase its knowledge of sensors.
For this phase we made a second seat but incorporated strain gauges into and onto the layup of the seat. These essentially measure how much the seat deflects by when in use. We then headed back to Nottingham and repeated the tests on the slider but this time recording the real life deflections on the seat.
These could then be compared to the simulated deflections in our computer model, allowing us to refine it and be more confident in any assumptions we made. This meant that we could remove even more material from where it wasn't needed and reinforce areas that added performance. The result was that the final seat we delivered to Emma was five times stiffer in key locations than her original and still 300g lighter.
This was an incredibly exciting and satisfying project to work on as I got to know Emma whose attention to detail and "no stone unturned" attitude to sport encouraged us to drive even harder.
The cherry on top was the trip I took to Paris to see my first Paralympic event, which just so happened to be watching Emma win another gold medal in VL2 using the seat that we had made.
Composites are a brilliant, but at times challenging, material to work with. They work well for making bespoke parts like adaptive equipment, but they often can't be treated in the same way as metals or plastics can, in terms of joining them to a boat. This is the main 'easy win' we witnessed when looking at Paralympic GB's equipment and so alongside a new seat for Emma, I created a best practice guide for composite equipment for the team to hopefully leave one fewer stone unturned for them too.
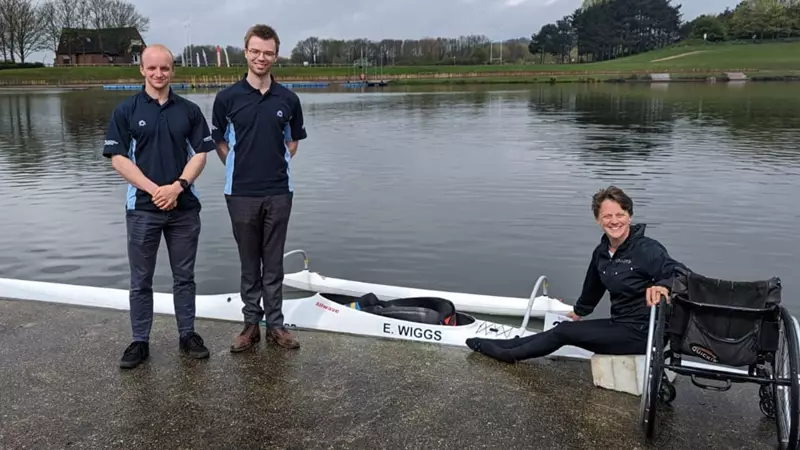